
- #Phan mem midas gen full#
- #Phan mem midas gen pro#
- #Phan mem midas gen software#
- #Phan mem midas gen free#
drag & drop)Ĭlear structure according to the object area (dies, machines, material etc.), process area (forming operations) and graphic model / results areaĪFS technology (application function sets) simplifies use The most significant advantages of the hands-on and user-optimized graphical user interface (GUI) are:Įasy, intuitive Windows style user interface (e.g. Simufact Forming stands out due to its easy-to-use design and the fact that it only takes a short time to become familiar with it. With a few clicks, all standard-forming processes can be simulated and evaluated.
#Phan mem midas gen software#
Simufact Forming's standard user interface allows for the software to be easily used and therefore, to become an engineering tool for developers of dies or processes whose daily work is supported and simplified. Simufact Forming is application-oriented as well as easy and fast to master. He does not have to deal with the physics of the forming process, nor with simulation-specific details. This is not the case with Simufact Forming: The user can focus on the engineering-related details of the forming process. The operation of simulation software very often requires a lot of expert knowledge to build up and program complex models. Our customers confirm the fact that we have achieved a lot in this field. Our goal is to focus the software to the practical needs of the users. Simufact Forming is a simulation tool for hands-on professionals working with forming technology.
#Phan mem midas gen pro#
MasterFrame Pro will automatically apply the wind loading to all members, perpendicular to each panel.MSC Simufact Forming 15.0 | File size: 3.3 GB
#Phan mem midas gen full#
MasterFrame frame loading diagram displays the final loads that are applied to the structural member together with their values and direction, giving you full graphical validationĪt steel design time, appropriate loading cases are automatically selected for the design of the member, with regard to differing wind diagonal values The weighted pressure coefficients for panels are multiplied by the appropriate dynamic pressure q value taking into account wind direction, diagonal length, crosswind breadth and height above ground level Up to 8 wind directions can be considered in a model

User control to override the automated panel zoning or Cpe value Internal pressure and suction coefficients can be added for each direction
#Phan mem midas gen free#
Goes beyond the basics to handle, parapets, canopies, free standing structures and open sided structuresĮnter the distance to any adjacent structure to automatically accommodate funneling effects Simply enter the UK or Irish national grid reference, or pick on the map to calculate the wind site pressure Included in the core modelling module of the Building Design SuiteĬonsideration of dynamic augmentation factor or structural factor CsCd when considering the overall stability of the structure
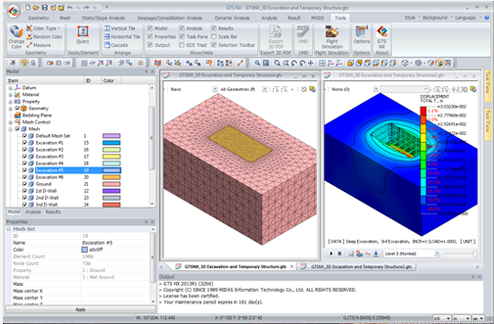

Your wind loading application is now complete location maps, or input your Grid Referenceīasic site information for anywhere else in the world can be added to the libraries

Using the MasterFrame Pro, set the main bracing members into wind diagonal groupsĪutomatically generate wind panels using the MasterFrame Pro softwareĪt this stage all zones and Cpe values are automatically determinedĮstablish the wind pressure by simply picking your building location from the built-in GB & Ireland O.S. Specify the wind directions you want to consider, i.e. With MasterKey Wind Analysis you can reduce the time-consuming process of calculating and applying wind loads on a building to a few simple steps as follows: MasterKey Wind Analysis used with MasterFrame Pro makes light work of the complex task of applying wind loading to any structure complete with automatic wind site pressure calculation, full wind zoning and calculation of pressure coefficients for absolutely any wind direction. MasterKey: Wind Analysis is the structural software every engineer has been looking for to dramatically reduce the burden of wind application on a frame to either BS 6399 Pt 2 or EC1 – 4, making the accurate application of wind loads a very simple and virtually automated task.
